Finished Goods Inspections
Finished Goods Inspections across 76 Countries
Finished Goods Inspections - Goodadas online inspection platform gives you a complete range of supply chain quality control inspections for your supplier or factory. All our finished goods inspections include a detailed report documenting all the findings, which are available to you on-line.
A Finished Goods Inspection usually takes place at the sellers warehouse. The goods need to be ready for shipping or have a minimum of 80% completed. This inspection is a visual check of specifications, quantities, dimensions, packing requirements and shipping marks. During this inspection any on-site testing can be conducted or samples can be collected to be independently tested. Our Inspectors can check products in over 76 countries.
Avoid paying suppliers for goods that do not match your specifications. Save money and time buying incorrect goods. Have them visually inspected before they leave the Seller.
Why have Quality Control Inspections conducted at the Factory?
-
Reduced costs due to Product Failure - for example, replacement and disposal of faulty goods.
-
Reduced days lost due to production delays.
-
Maintain full control of the quality of your product.
-
Improved communications with the Supplier.
-
Reduce nonconforming or defective products.
-
Improve your supplier manufacturing standards.
-
Pay only for conforming goods.
-
Reduce Customer complaints on faulty products.
Finished Goods Inspection Explainer Video
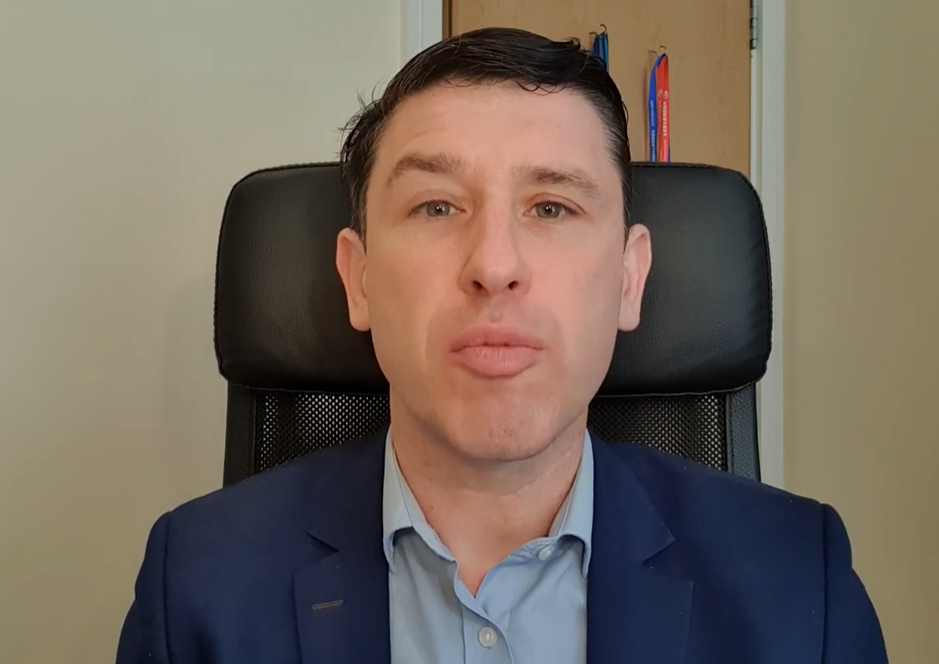
Click on the Image to play the video
|
For more information about Finished Goods Inspections, please contact:
Contact Person: Aidan Conaty
Mobile- Messenger (Click to Connect)
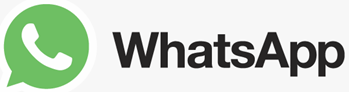
Laptop / PC (Click to Connect)
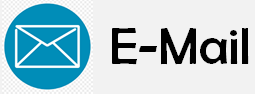
Phone:(Europe/ Rest of the World) +353 1 885 3919 ; (UK) +44.020.3287.2990 ; (North America) +1.518.290.6604
Critical Reasons for a Finished Goods Inspection
1. Reduce the Risks
Finished Goods Inspections will reduce the risks of a failed product reaching your warehouse, marketplace, and customers. You will avoid a customer’s complaints about faulty products and maintain your brand name.
2. Reduce the Costs
Finished Goods Inspections will ensure that you avoid paying for incorrect products. These would include - Supplier balance payments, transport costs, product replacement, and disposal.
3. Maintain Quality
Your supplier will know that you are monitoring their manufacturing processes and the quality of your products. It will reduce time delays and ensure that Product Standards are maintained.
What is checked during a Finished Goods Inspection?
-
Quantity - Sampling Size is determined by standards set out by our Acceptable Quality limits. Please visit our AQL page to determine how many samples of the product the Inspector will need to check. Having a Finished Goods inspection conducted at this stage means 80% of products will be finished and packed, and 20% unpacked. All inspections are conducted under the internationally recognized standard of ANSI/ASQC Z1.4 (ISO 2859-1).
-
Dimensions - The Inspector will record the dimensions of your product to confirm they meet your dimensional standards.
-
Color - The Inspector will visually inspect your products color using color code charts provided by the supplier or other color checking devices.
-
Weight - During the inspection, the Inspector will weigh both packed and unpacked products and record the findings in the inspection report.
-
Art Work/Logos - The Inspector will examine all samples, take images of any artwork or logo, and compare it to any the reference sample.
-
Accessories/Assembly Instructions - The Inspector will check all accessories or assembly instructions conform to the clients requirements.
-
Packaging - The Inspector can carry out checks on the packaging to determine if it meets all conditions agreed between the Supplier and the Buyer. Checks can include labels, barcodes, dimensions, and weight details, etc.
-
Shipping Marks - The Inspector can check that the shipping marks match the client's requirements.
-
Onsite Test - The Inspector can check any product functionality, label barcode scanning, and record a demonstration of the product being tested. Any other additional onsite tests requests can also be carried out.
-
Workmanship - The inspector will examine all samples for any defects or nonconformities such as scratched surfaces, broken parts, poor surface finish, functionality checks, indentations or any other defect that could affect the saleability of the product.
-
Report - A detailed report will be completed and sent to a customer within 24 hours* after the inspection date. The report will include photos from the inspection and images of any defects accompanies by the inspector remarks and the inspection result.
-
Other Suggestions - A Buyer should always plan for unforseen events or worst-case scenario. What if a Supplier delays an inspection or the result of inspection is a "Fail". You should build in a sufficient number of days between the inspection date and the shipping date. Always Plan for the unexpected!!
How to order inspections on-line?
Step 1 - Customer fills out an online inspection request form.
Step 2 - Inspection coordinator confirms the inspection request and assigns an inspector to your inspection.
Step 3 - Customer makes payment for inspection.
Step 4 - Inspector then visits the factory and follows inspection protocol as per inspection order details.
Step 5 - Inspection coordinator will review and upload inspection report within 48 hours of inspection date.*
Step 6 - Client can download and review report, plus request a call back to discuss inspection report and result.