Types of Inspections
Third-Party Inspection Services
Goodada inspections are designed to provide you with solutions to all areas of your quality control management. We tailor every inspection to meet your specific QC requirements. Your assigned inspection supervisor will work closely with you to ensure that every check or audit meets your requirements.
A Finished Goods Inspection (Pre Shipment Inspection PSI) is the most critical inspection which confirms the complete order quality levels. A Finished Goods inspection requires 80% of goods to be completed and be packed. Samples of the goods are randomly selected using the internationally recognised AQL standard for sample selection. There should be a 3-5 day window between this inspection and the container being loaded. To find our more, please visit our Finished Goods Inspection page.
During a Container Loading Inspection, an Inspector will inspect the loading process, the condition of the container, the quantities of the product, ensure the proper handling of your goods as they are being loaded. All stages of the loading process are recorded. Final payment should only be released after this report, and a copy of the Bill of Lading has been received. Please visit our Container Loading Inspection page to learn more.
An Inbound Cargo Inspection checks the goods when it arrives at its final destination, usually a port or a warehouse facility. The terms of most purchase contracts require goods to be checked when it lands at a vendor's designated warehouse or holding facility. This service is also used when there is a dispute between the seller and vendor over quality or quantity issues. For additional information, please visit our Inbound Cargo Inspection page.
An Inspector will remain at the factory throughout the production process. This inspection is suitable for companies that require continuous updates to ensure that production timelines and quality control checks are maintained and recorded. An Inspector will monitor the production schedule, supervise the factory's internal quality control, conduct random inspection from raw material to the finished products and report to you every day. To learn more, please visit our Production Monitoring page.
This inspection is very popular with clients who are experiencing communication difficulties with their supplier.
A During Production Inspection focuses on the processes and products being produced so that any problems can be uncovered at an early stage. It maintains a communication channel between the supplier and the client. The client will be updated on timelines and if any issues are arising. To get more information, please visit our During Production Inspection page.
An Early Production Inspection focuses on the Raw Materials that are to be used to manufacture the products. With this inspection, samples of the raw materials can be collected and sent to a laboratory for testing to confirm standards and requirements. To find our more, please visit our Early Production page.
A Factory Audit will verify your supplier and provide you with a complete and detailed understanding of your supplier's production capacity capabilities, quality control practices and procedures, and their day to day operating and management procedures. The Factory Audit will help you select a supplier who meets your requirements to uncover problems before production or order confirmation. Please visit our Factory Audit page to get more information
A supplier audit is when a third-party inspector visits a supplier’s warehouse, factory or processing facility to review and check its practices, processes, certification and trading history. To learn more, please visit our Supplier Audit page.
A Buyer verification checks that a buyer is legitimate and is capable of being a suitable customer for your company. Our inspectors will visit the buyers office and warehouse to review their business and trade levels. For additional information, please visit our Buyer Verification page.
A robust code of conduct should include a term that states that it is a requirement for a third-party agency, appointed by the company, to visit the Supplier or Buyer to check that they are adhering to the Code of Conduct. To learn more, visit our Code of Conduct Audit page.
A shipment of your products arrive at its final destination. Your customer discovers that there are issues, defects or missing parts with the order. Your customer notifies you that there is a problem, and you must immediately fix it. What can you do to resolve this issue? Many firms use Goodada's Quality Sorting Service to sort the problem out. To find out more visit our Quality Sorting page.
For more information about our Third Party Inspection services contact:
Contact Person: Aidan Conaty
Mobile- Messenger (Click to Connect)
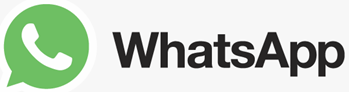
Laptop / PC (Click to Connect)
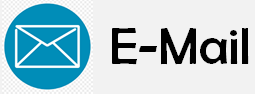
Phone:(Europe/ Rest of the World) +353 1 885 3919 ; (UK) +44.020.3287.2990 ; (North America) +1.518.290.6604
Goodada inspects the following products
Hard Goods
|
Electrical & Electronical
|
Kitchenware |
Home Appliances |
Household Utensils |
Lights & Lighting |
Furniture |
Electrical Tools |
Furnishings |
Telephones & Parts |
Porcelain & Ceramics |
Transformers |
Toys & Gifts |
Electronic Accessories |
Seasonal Products |
Computer Parts |
Sports & Entertainment |
|
Stationary |
|
Office Supplies |
|
Fashion & Jewellery |
|
Clocks & Watches |
|
Eyewear & Binoculars |
|
Tools & Equipment |
|
|
|
|
|
Soft Goods
|
Mechanical
|
Fabric |
Machinery Parts |
Apparel |
Metal Sheets |
Garment Accessories |
Plastic Film |
Home Textiles |
Packaging |
Footwear |
Paper |
Leather Goods |
Construction Products |
Luggage & Bags |
|
Caps & Headwear |
|
Sporting Goods |
|
|
|
|
|
Food
|
Other
|
Seafood |
Chemicals |
Fruit |
Minerals |
Grains & Wheat |
Scrap Metal |
Meats |
|
Processed Food |
|
Frozen Food |
|
Confectionary |
|
|
|