During Production Inspection
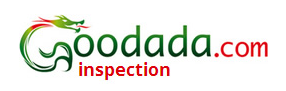
During Production Inspection Services
During Production Inspections will give you a complete overview of production and expected completion times, thus avoiding costly stock outs. A During Production Inspection will allow you to see the production line in action and explore some possibilities to improve production times and processes.
Avoid the surprise conversation with a supplier who informs you that there is a delay or issue with your order. A During Production Inspection will "Buy You Time" to resolve any production issues and/ or find alternative supply solutions before you have no stock for your customers.
Why have Quality Control Inspections conducted at the Factory?
-
Reduced costs due to Product Failure - for example replacement and disposal of faulty goods.
-
Reduced days lost due to production delays.
-
Maintain full control of the quality of your product.
-
Improved communications with the Supplier.
-
Supplier can quickly fix any product issues identified during inspection.
-
Payment can be issued for conforming goods after the goods have passed an inspection.
-
Reduce Customer complaints on faulty product.
For more information about During Production Inspections, please contact:
Contact Person: Aidan Conaty
Mobile- Messenger (Click to Connect)
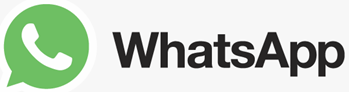
Laptop / PC (Click to Connect)
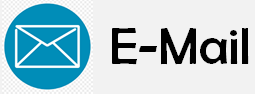
Phone:(Europe/ Rest of the World) +353 1 885 3919 ; (UK) +44.020.3287.2990 ; (North America) +1.518.290.6604
Benefits of a During Production Inspection
-
A During Production Inspection will improve the communication between you and your manufacturer as an inspector on-site will be able to communicate your requirements to the manufacturer.
-
Avoid the "If only I knew earlier" statement. During Production Inspections will give you a complete overview of production and expected completion times, thus avoiding costly stock outs.
-
A During Production Inspection will allow you to see the production line in action and explore some possibilities to improve production times and processes.
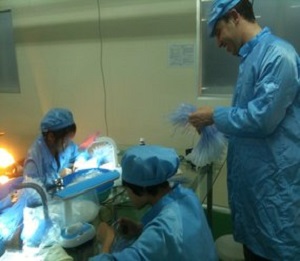
What is covered in a During Production Inspection?
As per standard inspection protocol Goodada inspect the following, but customers can also add additional request. We are also happy to tailor inspection checks so please ask for further details.
-
Quantity - Sampling Size is determined by standards set out by our Acceptable Quality limits. Please visit our AQL page for more to determine how many samples inspector will check of your order. Having a During Production inspection conducted at this stage means products will be still in mid production and some products will be finished and no products are packed.
-
Dimensions - inspector will record dimensions of your product to confirm they meet your dimensional standards.
-
Colour - inspector will visually inspect the colour of your product using colour code charts provided by supplier or other colour checking devices.
-
Weight - during inspection inspector will weigh both product packed and unpacked to determine if they have met customer standards.
-
Art Work/Logos - inspector will examine all samples and take images of any art work or logo and compare to reference sample.
-
Accessories/Assembly Instructions - majority of products have additional components or documents. The Inspector can check and compare to a reference sample.
-
Packaging - inspector will carry out strict checks on all samples packaging to determine if they meet all conditions agreed between supplier and buyer.
-
Shipping Marks - inspector will check shipping marks are correct as per clients standards.
-
Onsite Test - inspector will check functionality, barcode scanning and assembled products to confirm they meet clients requirements. Any additional onsite request can be also be carried out.
-
Workmanship - inspector will examine all samples for any defects or nonconformities such as scratched surfaces, broken parts, poor surface finish, indentations or any other defect that could affect the saleability of the product.
-
Report - a detailed report will be complete and sent to a customer within 48 hours* of inspection date. Report will include images of inspection findings mentioned above, inspector remarks and inspection result.
-
Sample Report - click here for a sample report